Chillers in hospitals keep energy costs down
Dec 27, 2013
Chillers are critical to the daily function of a health facility. But what’s even more important than having chillers in hospitals or clinics? Having the right chiller. Reliability, efficiency, and facility fit all have to be considered before going chiller shopping. The right chiller can make all the difference in reducing energy costs, while a sub-par piece of equipment can actually increase costs by leading to shortened equipment life span or even equipment failure. Here are some simple tips that should inform your search on one of the most integral ingredients for effective health facility commissioning.
Know your needs
Buying a chiller is expensive, no matter how you slice it. Installation costs can run exorbitantly high for such a heavy, expansive piece of equipment (sometimes even requiring a crane to place within a building!). Your structure should be exhaustively evaluated for a chiller that suits your price range as well as your structure. Facility volume, layout, and required BTUs all need to be considered, and the only way to know for sure what kind of chiller a facility needs is with an expert’s assessment. Going with the first one you see, or worse, the most economical option, could end up costing you much more than it will save you.
Avoid older scroll compressors
Older varieties of “scroll” type compressors only have two modes, on and off. Ergo, these machines operate within a temperature range: when the temperature rises too high, they start chilling the area, and when it drops to the end of its range, it disengages. Forcing the machine to constantly whir to life multiple times per day actually raises energy consumption rates compared to digital models or inverter scroll compressors. The clear superior choice, these newer models are capable of idling at a low-energy rest state and maintain much more precise temperature ranges.
Get it reboot-ready
When emergency power kicks in during an unplanned outage at a medical facility, the transition has to be seamless. Unfortunately, not all chillers are built for instant switch-over – some take 15 minutes or more to come back online. In a work environment where instantaneous energy is a must, your chiller needs to be able to deal with anything thrown at it at the drop of a hat.
Consider heat recycling
One byproduct of all chiller systems is thermal energy. Traditionally, this heat is just filtered up and away from the building via vents, but recycling it back into the facility could curb energy costs from other sources around the building dramatically. The hot refrigerant vapor has a plethora of uses, from using it to heat space around the building, warm the reheat coils in parts of the air conditioning systems, or even be for personal use in the restroom, laundry area or kitchen.
Take advantage of ambient air
Since 2010, more energy-efficient, “free cooling” chillers have been looked upon extremely favorably by facilities looking for commissioning services. These types of chillers use cold outside air as a tool for chilling water – a strategy best suited for regions with enduring, predictable cold seasons. The method is ingeniously simple: when the outside temperature falls below a predetermined point, a valve opens and allows chilled water to bypass the chiller it adjoins. This water is then directed through a special “free cooling” coil that puts the gratis gift from nature to good use throughout the facility.
You may be interested in these other posts:
- How hospitals are reducing energy consumption with existing building commissioning
- Hospitals prepare to reformat in light of Obamacare
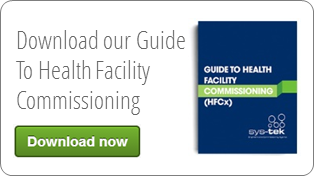